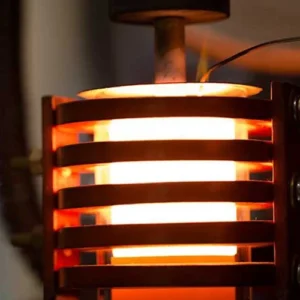
Why Choose Induction Technology?
XUVE Electronic has successfully applied electromagnetic induction technology across various industries for melting, heating, and welding operations. But why should you consider induction technology, and how does it differ from other heating methods?
For most engineers, induction is an exceptional heating solution, offering precision, efficiency, and reliability. For those unfamiliar with induction heating, witnessing a metal bar heat to glowing red within seconds inside a coil is often a fascinating experience.
Although induction heating systems involve specialized fields such as physics, electromagnetics, power electronics, and process control, the fundamental concept of induction heating is remarkably simple and easy to understand. This simplicity, combined with its advanced capabilities, makes induction technology a compelling choice for modern industrial applications.
Basic Principle
Discovered by Michael Faraday, induction uses a conductive coil, like copper, to generate a magnetic field when current flows through it. The field’s efficiency depends on the coil design and the current intensity, forming the foundation of induction heating technology.
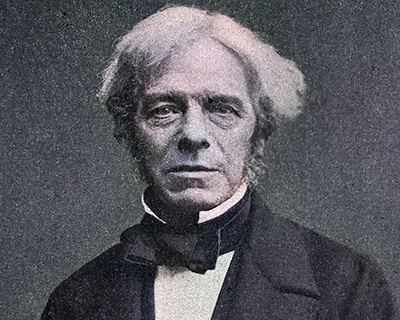
Magnetic Field Dynamics and Induction Heating
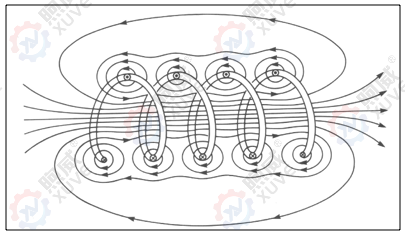
The direction of a magnetic field depends on the direction of the current. In the case of alternating current (AC), the changing direction of the current causes the magnetic field to reverse direction at the same frequency. For instance, a 60 Hz AC current results in the magnetic field switching direction 60 times per second, while a 400 kHz AC current leads to 400,000 direction changes per second.
When a conductive material (the workpiece) is placed within a changing magnetic field, such as one created by AC current, a voltage is induced in the material according to Faraday’s Law. This induced voltage causes the flow of electrons, generating a current in the workpiece. Notably, the direction of this induced current is opposite to the current in the coil. This means we can control the frequency of the current within the workpiece by adjusting the frequency of the current in the coil.
As the current flows through the material, the movement of electrons encounters resistance, which generates heat—this is the Joule heating effect. Interestingly, while greater resistance typically produces more heat, induction heating can also effectively heat highly conductive materials like copper. This unique capability is a cornerstone of the versatility and efficiency of induction heating technology.
What Are the Key Elements of Induction Heating?
Induction heating requires two fundamental elements:
1. A Changing Magnetic Field
This is typically produced by alternating current flowing through a coil.
2. A Conductive Material
A workpiece made of conductive material is placed within the magnetic field to induce current and generate heat.
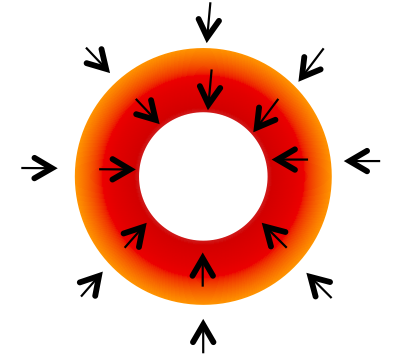
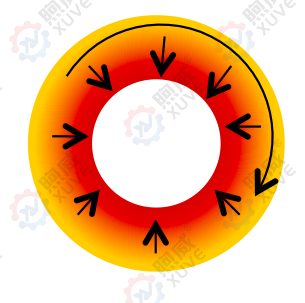
How Does Induction Heating Compare to Other Methods?
There are many non-induction methods for heating materials. Common industrial practices include gas furnaces, electric resistance heaters, and salt baths. These methods transfer heat to the product primarily through convection and radiation, where a heat source (burner, heating element, or liquid salt) heats the product’s surface. The heat then spreads throughout the material via thermal conduction.
Induction heating, on the other hand, does not rely on convection or radiation to heat the product’s surface. Instead, heat is generated directly within the product by the flow of induced currents (eddy currents) on the surface. This surface heat then transfers through the material by thermal conduction. The depth of heat penetration depends on a parameter known as the electrical reference depth.
The electrical reference depth is largely determined by the frequency of the alternating current in the workpiece. Higher frequencies result in a shallower depth of heat penetration, while lower frequencies allow for deeper penetration. This depth also depends on the electrical and magnetic properties of the workpiece material.
This direct and precise method of heating provides significant advantages in efficiency and control over traditional heating methods, making induction heating ideal for a wide range of industrial applications.
XUVE Electronic: Tailored Heating Solutions
XUVE Electronic leverages these physical and electrical principles to create customized heating solutions for specific products and applications. Through precise control of power, frequency, and coil geometry, XUVE Electronic designs equipment with exceptional process control and reliability across a wide range of industrial applications.
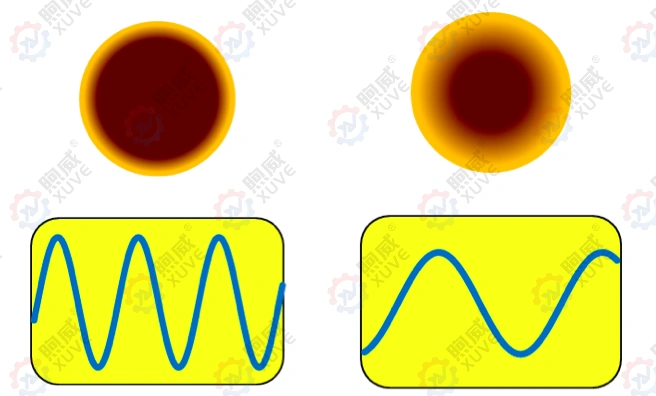
Induction Melting
For many processes, the first step in producing a usable product is melting, and induction melting provides a fast and efficient solution. By modifying the geometry of the induction coil, induction melting furnaces can accommodate charge sizes ranging from as small as a coffee cup to several hundred tons of molten metal. Additionally, by adjusting frequency and power, XUVE Electronic can process nearly all metals and materials, including but not limited to iron, steel, stainless steel alloys, copper and copper alloys, aluminum, and silicon. Each induction system is custom-designed for specific applications to ensure maximum efficiency.
Advantages of Induction Melting: Inductive Stirring
A significant inherent advantage of induction melting is inductive stirring. In an induction furnace, the metal charge material is melted or heated by currents generated by an electromagnetic field. Once the metal becomes molten, this field also causes the molten bath to move, creating what is known as inductive stirring. This constant motion naturally mixes the molten bath, resulting in:
· A more homogeneous mixture of the molten material.
· Improved alloying, as the stirring evenly distributes elements throughout the melt.
The degree of stirring is determined by factors such as the furnace size, the power input into the metal, the frequency of the electromagnetic field, and the type and amount of metal in the furnace. For specific applications, the amount of inductive stirring can also be finely controlled and adjusted to meet specialized requirements.
XUVE Electronic’s induction melting solutions are designed to deliver unmatched efficiency and performance for diverse industrial needs.
Induction Vacuum Melting
Induction heating relies on magnetic fields to generate heat, making it possible to use refractory or other non-conductive materials to isolate the workpiece (or charge) from the induction coil. The magnetic field passes through these materials, inducing voltage in the charge. This allows heating to occur in a vacuum or under a controlled environment. Such conditions enable the processing of reactive metals (e.g., titanium, aluminum), specialty alloys, silicon, graphite, and other sensitive conductive materials.
Precision Induction Heating
Unlike some combustion methods, induction heating offers precise control regardless of batch size. By adjusting the current, voltage, and frequency in the induction coil, the heating process can be finely tuned. This makes induction heating particularly suitable for applications such as surface hardening, quenching, tempering, annealing, and other forms of heat treatment. High accuracy is critical in industries such as automotive, aerospace, optical fiber, ammunition welding, metal wire hardening, and spring steel tempering.
Induction heating is also ideal for specialized applications involving titanium, precious metals, and advanced composite materials. Its unparalleled precision and control allow for seamless processes. Furthermore, using similar principles, such as vacuum crucible heating, induction heating can also be applied continuously in open-air environments—for example, non-oxidizing annealing of stainless steel tubes.
High-Frequency Induction Welding
Induction heating at high frequencies (HF) can also be employed for welding applications. In this case, the shallow electrical reference depth produced by HF currents is advantageous. For example, when forming a continuous metal strip, the strip passes through a series of precision-designed rollers that join its edges into a solid weld.
Before reaching the rollers, the strip passes through an induction coil. Here, the HF current flows along the “vee” shape formed by the strip edges, concentrating the current along these edges rather than the outer surface. This current heats the edges to an optimal welding temperature (below the melting point of the material). When the edges are pressed together, all debris, oxides, and impurities are expelled, resulting in a solid-state forge weld.
Future Applications of Induction Heating
With the rise of advanced engineered materials, the demand for alternative energy solutions, and the growth of emerging markets, induction heating offers a fast, efficient, and precise method for future engineers and designers. Its unique capabilities position it as a vital tool in addressing the heating challenges of tomorrow’s industries.